I decided to try one rib yesterday afternoon, after I got home from work. The ribs had been soaking for a couple of days, so I figured I'd see how I went with it. I had all the ribs numbered, so I thought I'd try rib number 13 first, that way I wouldn't feel so bad if it didn't work properly, and if it did, I'd feel more confident with the rest. There's also the fact that rib 13 is closest to the middle of the boat and so has the gentlest bends.
Well it didn't turn out. The main reason was not enough heat. I could only get the steam box up to 75C (167F), which isn't enough. Part of the problem was the camp stove I was using was struggling, it would boil the water, but only just. That improved when I put another gas canister in. Putting a styrofoam box around the steamer also helped, but I could still only get the temperature up to about 93C (199F). That's probably hot enough, but as soon as you take the wood out of the steamer, it starts to cool.
So I called it a day and did a bit more research on steam bending ribs. The general consensus on the QajaqUSA forum is that soaking the wood is a complete waste of time, since it'll take months for any moisture to really soak into the wood. It really comes down to the heat. You need to be able to get the wood up to boiling point, or very close, and bend it while it's at that temperature.
The best way to get the wood to boiling point was to actually stick it in the boiling water, so that's what I did.
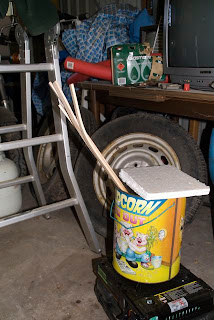
After a few failed attempts I finally managed to get a decent bend, as you can see from the next couple of pictures.
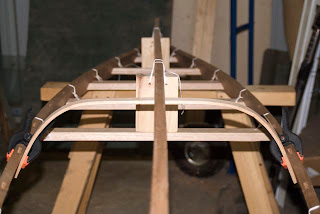
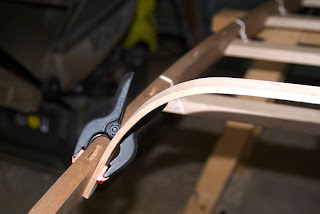
The trick is to keep the wood in the steam while you're bending it, and to bend it slowly. If you rush it you'll end up with a kink in the wood, and splinters. The splintering in the picture below isn't too bad, it hasn't really weakened the rib. Once it was dry and had cooled down, I shaved that part off with a 1" chisel. That part of the rib is slightly thinner than the rest, but some of the ribs are a little thicker than they should be anyway.
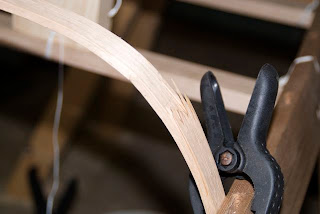
Because I can't get the whole rib into the boiling water, I found the best way to do each rib was one side at a time. I'd bend one side, clamp it to the gunwale and keelson, then when it had cooled I'd boil the other side and clamp the whole thing to the gunwales.
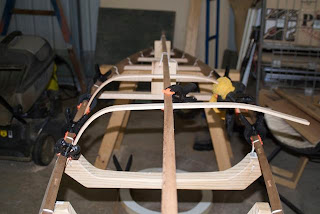
I found I was still getting some ribs breaking though, or at least splintering so much they weren't really useable. The reason for that is the grain in the material. If you look closely at the next picture, you can see the grain follows the bend in the wood, because it was straight to start with.
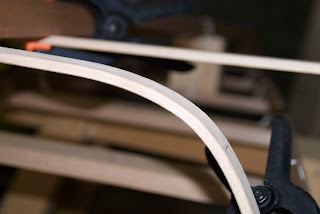
In the next picture, you can see where the grain doesn't quite follow the length of the wood, it's at a slight angle, and where that grain comes to the surface is where the rib is going to split.
This means I'm going to have to buy some more rib stock and be really choosy with what I buy this time.
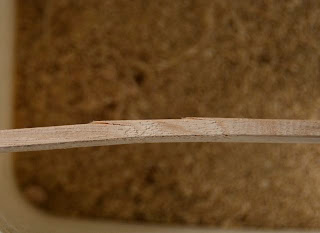
The next two pictures show some of the ribs after bending, already cut to length and fitted into the mortises. I think there's five of them finished. The only reason I haven't done more today is the gas ran out on the camp stove. We have an old gas barbecue I could use to heat the water, but I can't find the hose for it. I have about eight more ribs to bend that should bend okay, then I just have to buy the material for the rest.
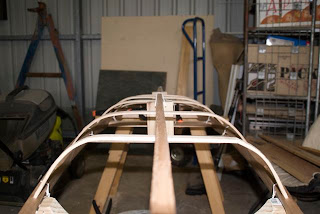
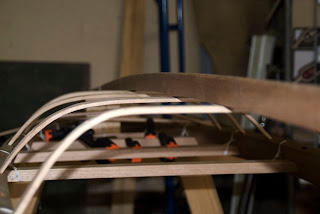
Once all the ribs are in place, they get lashed to the keelson, then the hull stringers are fitted and also laced to the ribs. That will be the hull finished, then there's just a couple of jobs to do on the deck and the coaming to bend and it'll almost be ready to skin.
I lost track of how much time I spent on the job today, since we had a visit from Donna's parents, but I'm guessing it was about three hours, which takes the total to 36 1/2 hours.